I am so sick of trying to drive solid rivets. I am not sure why I talked myself into it. Had I know how much it sucked I would have welded the fenders on. Drivers fender is fully riveted and welded to the rock rail. The passenger side is slowly getting riveted. I can only do a few before my elbows start to hurt from the air hammer. Once they start to hurt I jump to something else. I don't know if it is from where I broke my arms or just old age, but that air hammer puts a hurting on me.
This weekend was a bust. Got snagged up at work for the most part. Dean meet me at the local you pull it yard on Sunday. I got the 14 spoke wheels that he found in a junkyard by his house. Now I have 6 wheels and can mount up my tires. They also just dropped 4 TJs on the yard so I picked up a few things. I got all new seats. They had a couple of sets of the gray TJ seats so I picked the best ones and will replace the brown ones rather than getting things re-upholstered. I also got an air box, fuse box mount, transfer case shifter, parking brake cables, throttle cable, a couple shifter boots, and some misc. bolts that I was missing for the engine. So after a couple of hours on the yard I grabbed lunch and left for the shop.
I drove a couple rivets and then got started on the front suspension. I had planned for a custom build track bar, but found a nice unit on a grand cherokee at the junkyard. It is rubber bushings on both ends and has the right bends for the diff. I had to cut off the track bar mounts and move them about 1/2" to fit the new track bar. Then I jacked some coilovers from another build in the shop and started on the front shock mounts. 16" coilovers with some of the easiest mounts I have ever done. They layed right in.
Of course there had to be a snag. The coilovers were easy. Getting the fenders back on is a struggle. I have to clearance the fender for the shock hoop. This picture sucks, but a new camera is on the way so they should improve. I rolled some 18 gauge and welded it into the fender to clear the rear part of the hoop.
Then I could get the fender mounted up to determine the cutout for the coilover. I was sure this would be easy, but the shock hits the fender just wrong.
This hole fits the shock, but through travel the inside off the fender is hit. The plan is to cut out where the fender hits all the way down. Then roll some more sheetmetal and make a bolt on piece that goes to the inside of the coilover. I want it to unbolt so I don't have to remove the shocks to remove the fender. I also want it there to help keep mud out of the engine bay. I have had plenty of rigs that I just clearanced for the shock and called it good. They all worked, but I want something a little more polished this time around.
Then to finish off the day I also picked up a TJ brake booster and master. With a little bit of action with the drill I was able to bolt it in the same location as the original master. I will have to slightly modify the pedal to bolt up with the right travel and starting position. This will be simple, but I have to get the pedal out first. This also has a disc/drum proportioning valve and brake light switch installed so I feel like I make a leap in the right direction.
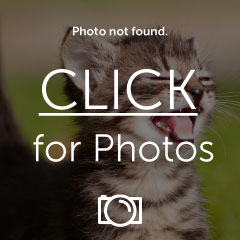