Well, this is sorta outside of the scope of ORSC but im going to document this here anyway. I made the decision to proceed with a "Large" CNC Rounter build. The goal of this machine is to cut wood(Fiancée wants new cabinet doors..) and possibly 1/4 aluminum plate.
Mechanical Stuff...
I have ordered the Ball Screws, Linear bearings, Anti Backlash Nuts and pillow bearings to began the design. I say begin the design because I'm using CHINA sourced hardware and I dont trust the drawings, so i am going to wait until i get the parts to be certain.
My Ballscrews and Linear Bearing should give me a machine size of ~ 35inches x 55inches. With a work area of something around 29x49. I am essentially going to rip off the design of a existing machine made by a company call Probotix.
I have a pile of "recycled" 80/20 here at work that I saved from the scrap bin, so that is the biggest reason i am building what i am.
My biggest challenge i see in this project is going to be the gantry supports, these are the beams that tie the base of the machine to top portion.
I will have solidworks models eventually but 3/4 aluminum plate plus machining isn't going to be cheap. So, I am still toying with the idea of 1/2 laser cut steel or using a piece of 80/20 for the upright.
Here are a couple close ups of the Probotix Machines x axis mechanics.
Spindle
My plan is to use a DeWalt 611 Router for my spindle first. I am using a 660 on my current machine and it hasn't shown any signs of wear, so the increased HP of the 611 and bigger bearings should not hurt. Eventually i might move to a watercooled vfd spindle but its not in the plans for now.
Something similar to this.
For the Motion Control portion, Im planning to use NEMA 23 motors @ 425oz each. This should give me a pretty strong range of motion (2@425oz) with 850oz on the y (long) axis. I might have to upgrade the x at some point but hopefully it will be adequate.
Software
I not sure yet which software route im going to go yet. There are 2 major options: Mach 3/4 which is windows based but requires purchase ($175) or Linux EMC CNC (free) both of these use the old school parallel port to bit bang the stepper drivers directly due to the critical timing requirements.
Mach 3
Linux CNC
But has many more custom GUI options.
That just about covers all of the "main" points.
O, Almost forgot. For the CAM software im using a "Demo" version of CAMBAM.
They have a unlimited trial they just limit you to how many launches of the software you use, so I keep it open in a VM and just suspend the VM when im not using it. I will likely buy it if i ever make a buck making something. Its pretty cheap $150.
Mechanical Stuff...
I have ordered the Ball Screws, Linear bearings, Anti Backlash Nuts and pillow bearings to began the design. I say begin the design because I'm using CHINA sourced hardware and I dont trust the drawings, so i am going to wait until i get the parts to be certain.
My Ballscrews and Linear Bearing should give me a machine size of ~ 35inches x 55inches. With a work area of something around 29x49. I am essentially going to rip off the design of a existing machine made by a company call Probotix.
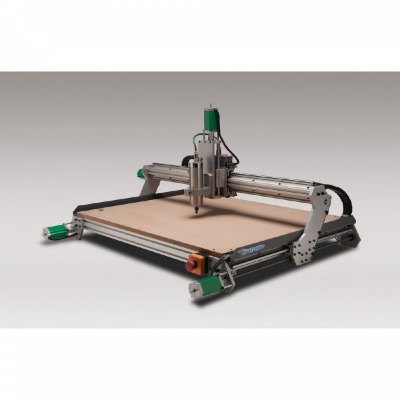
I have a pile of "recycled" 80/20 here at work that I saved from the scrap bin, so that is the biggest reason i am building what i am.
My biggest challenge i see in this project is going to be the gantry supports, these are the beams that tie the base of the machine to top portion.
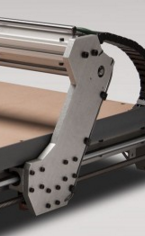
I will have solidworks models eventually but 3/4 aluminum plate plus machining isn't going to be cheap. So, I am still toying with the idea of 1/2 laser cut steel or using a piece of 80/20 for the upright.
Here are a couple close ups of the Probotix Machines x axis mechanics.
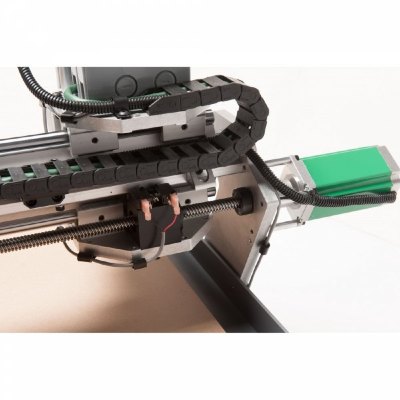
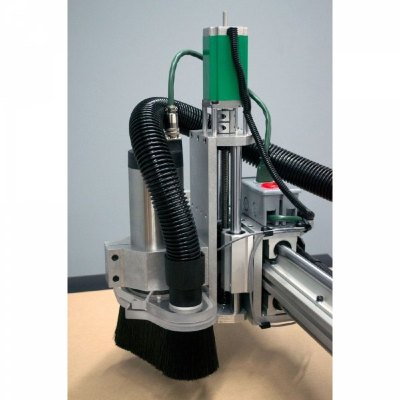
Spindle
My plan is to use a DeWalt 611 Router for my spindle first. I am using a 660 on my current machine and it hasn't shown any signs of wear, so the increased HP of the 611 and bigger bearings should not hurt. Eventually i might move to a watercooled vfd spindle but its not in the plans for now.
Something similar to this.
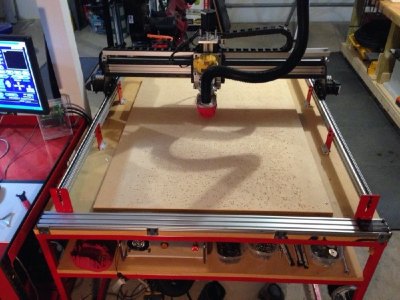
For the Motion Control portion, Im planning to use NEMA 23 motors @ 425oz each. This should give me a pretty strong range of motion (2@425oz) with 850oz on the y (long) axis. I might have to upgrade the x at some point but hopefully it will be adequate.
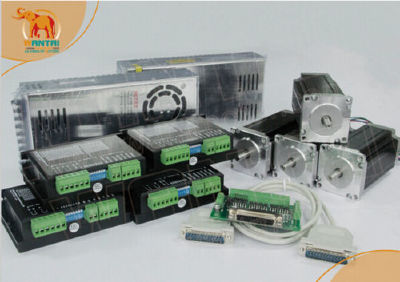
Software
I not sure yet which software route im going to go yet. There are 2 major options: Mach 3/4 which is windows based but requires purchase ($175) or Linux EMC CNC (free) both of these use the old school parallel port to bit bang the stepper drivers directly due to the critical timing requirements.
Mach 3
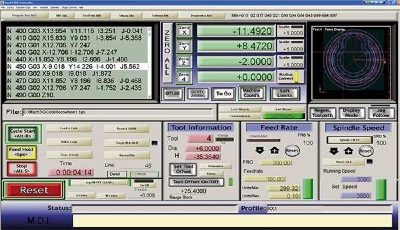
Linux CNC
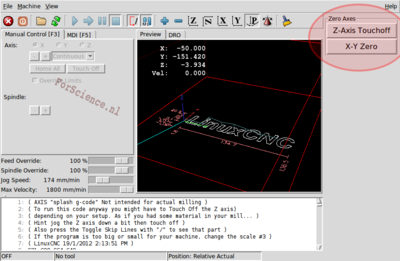
But has many more custom GUI options.
That just about covers all of the "main" points.
O, Almost forgot. For the CAM software im using a "Demo" version of CAMBAM.
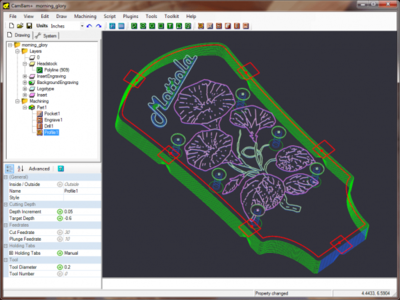
They have a unlimited trial they just limit you to how many launches of the software you use, so I keep it open in a VM and just suspend the VM when im not using it. I will likely buy it if i ever make a buck making something. Its pretty cheap $150.
Last edited: